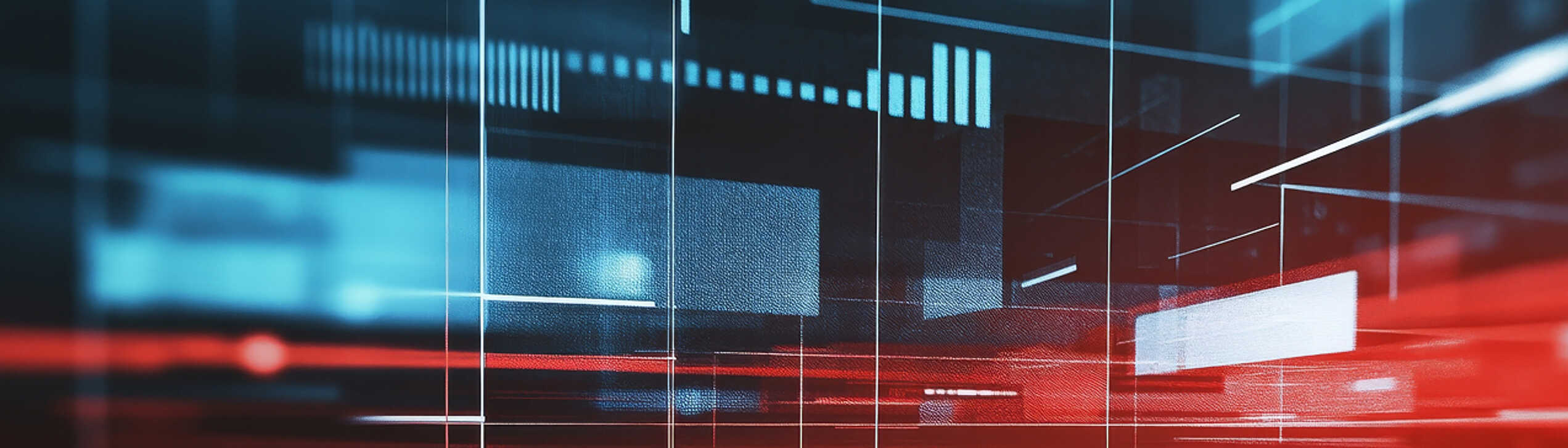
Continuous Mixer GCM
Continuous mixing of powders, granules and liquids
The continuous GCM mixer is suitable for mixing a wide range of powders, flakes and granulates and viscous products, also in combination with spraying of liquids. The GCM family covers a wide range of capacities (1 – 100,000 kg/h) and is used in the plastics, chemical, pharma and construction chemical industries amongst others. For the food industries, special models have been developed which enable short cleaning times. The continuous gravimetric supply of the starting materials into the GCM mixers is realised using loss in weight feeders, another Gericke field of expertise.
For more information:
InquiryOutstanding mixing efficiency
Continuous mixing processes are a powerful alternative to traditional batch processes. They combine mixing efficiency and high throughput with low space requirements. The continuous process consists of automatic gravimetric feeding of the starting ingredients which are precisely and continuously metered into the compact continuous GCM mixer. Capacities range from pharmaceutical applications (oral solid dosage: 1 – 1000 kg/h), through chemical and food applications (several 100 kg/h to 20 000 kg/h), right up to large capacity mixing of plastics upstream of extrusion (100 t/h).
Integration of liquids for plastic, chocolate and cereal bars
The GCM is not only used for the mixing of powders and granules, but is also excellently suited for the integration of liquids into a solid stream, e.g. adsorption of liquids to silica. The mixing family consists of U-shaped or tubular mixing chambers. Jacketed executions are used for plastic and chocolate/cereal bar applications. Special executions have been developed for some advanced requirements of the nutritional industry. The mixing paddles can be slid out of the mixing chamber to give optimal access for cleaning.
The fundamentals of continuous mixing, covering both the aspects of required feed precision and the mixer design, have been investigated with some of the world’s leading technical universities, e.g. ETH Zurich, Technical University of Munich, Ecole de Mines d’Albi, Rutgers University.
Your benefits
- Gericke delivers the complete feeding mixing installations.
- The GCM mixers achieve a very high degree of mixing, even for micro ingredients.
- Continuous mixers can be easily integrated in downstream continuous processes like extrusion or filling, packaging or a tableting line.
- Special execution for mixing of solids with liquid streams.
- Risk of demixing downstream of the GCM mixer is reduced since intermediate buffers can be avoided.
- Low space requirements even with large throughputs.
- Hygienic and pharmaceutical models (optional).
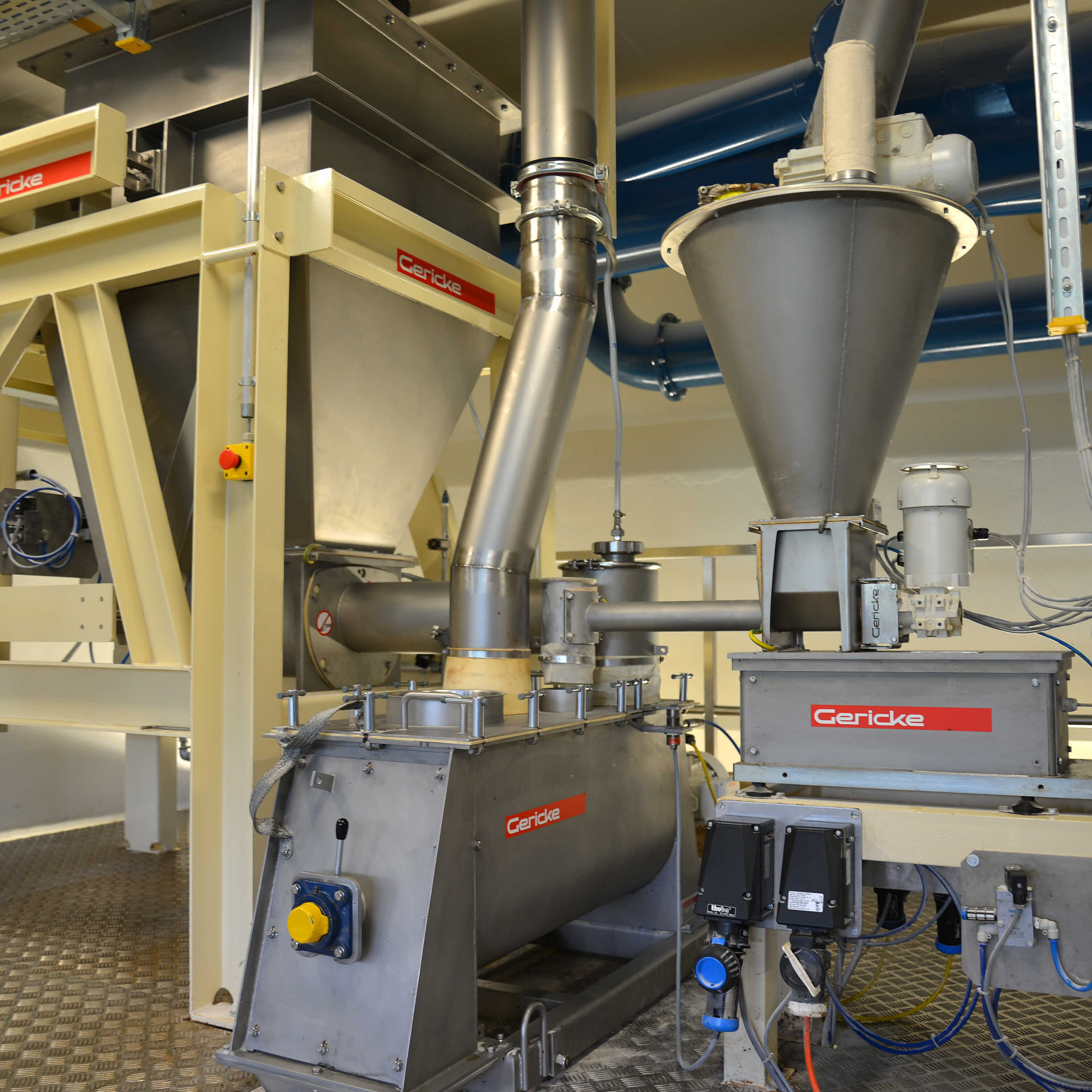
Applications
Solids-solids blending
Product properties such as very fine, wide particle size distribution or variable specific density can be handled. With the optimum ratio of mixing volume to throughput the mixing process is gentle, fast and respects the different properties of the bulk material.
Mixing of solids with liquids
Liquids are sprayed onto bulk as chemical additives (absorption aromes, binding agents). The prime concern is preventing the formation of agglomerates, absorption or liquid binding with the product. Mixer size, number and location of spray nozzles and residence time are fully customizable.
Mixing of liquids with solids
GCM mixers are suited to blend a stream of solids into bigger stream of liquids. Examples are the viscous mass preparation in cereal bar production or chocolate upstream filling lines. In ceramic production GCM mixers are used upstream kneading or extrusion.
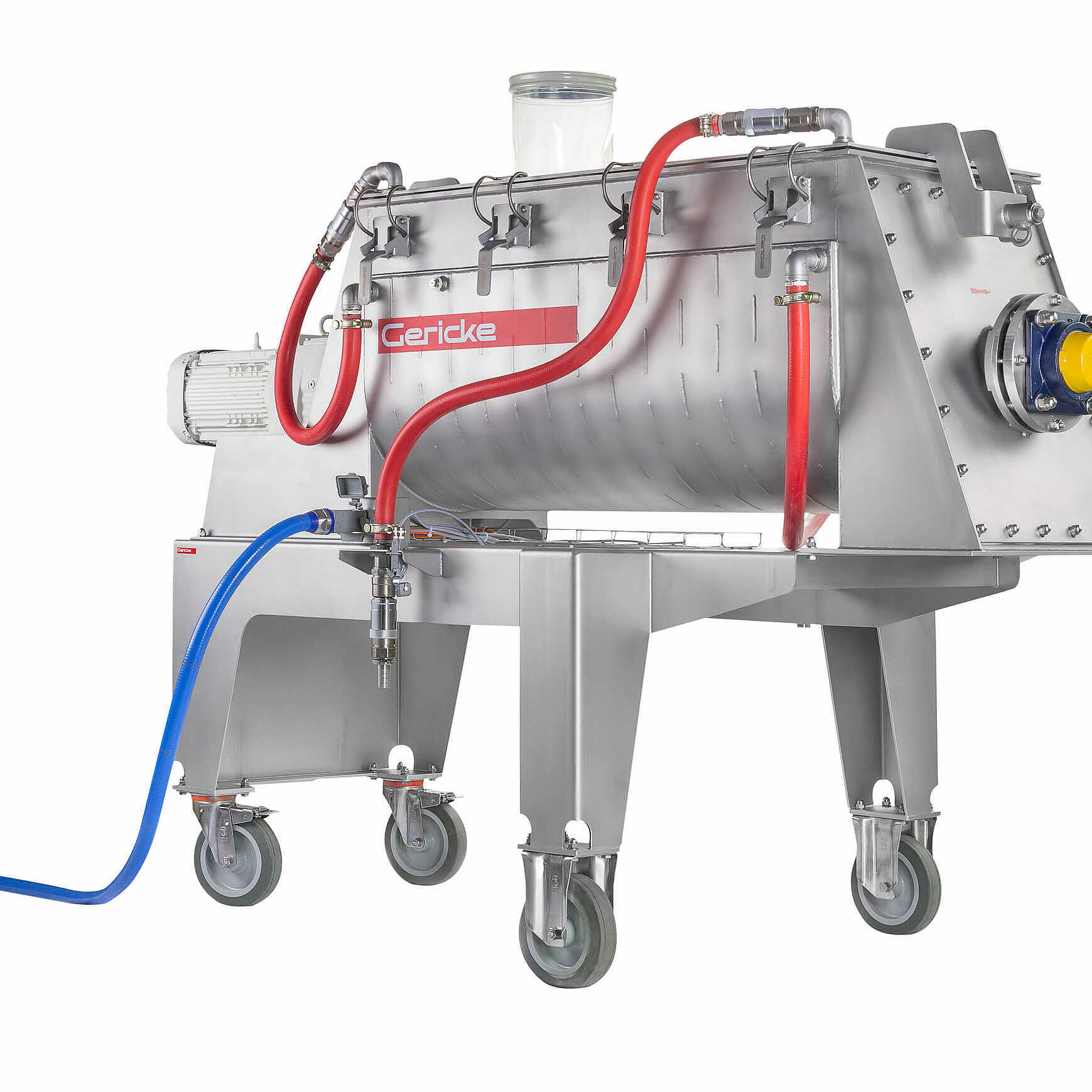
Specifications
- For ranges from 10 l up to 150,000 l/h
- Round or U-shaped mixing chamber
- Available with heating/cooling jacket and overpressure housing
- Optional extractable cantilevered drive “ECD”
- ATEX and IECEx Categories 1, 2 or 3
- FDA and EG 1935/2004 certificates available
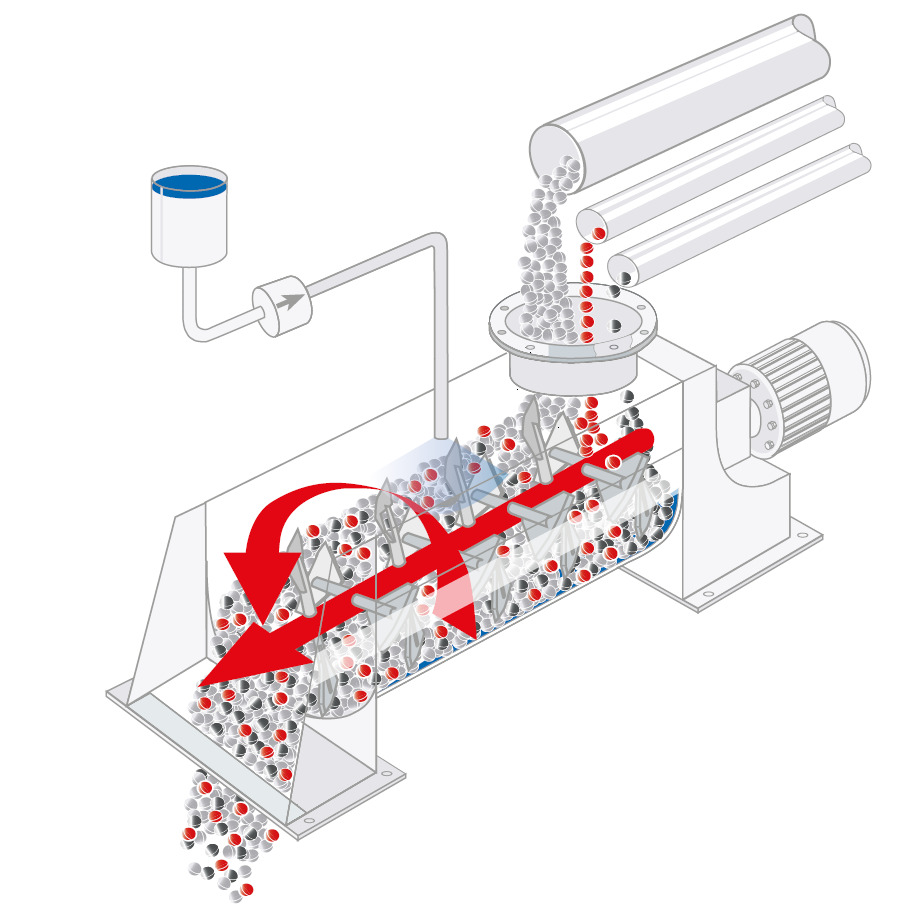
Principle of operation
The infeed ingredients are continuously weighed by GERICKE feeding systems and added into the mixing chamber in accordance with the recipe. GCM continuous mixers offer the optimum combination of radial and axial mixing (dispersion).
For more information:
Expertise. Value. Trust.