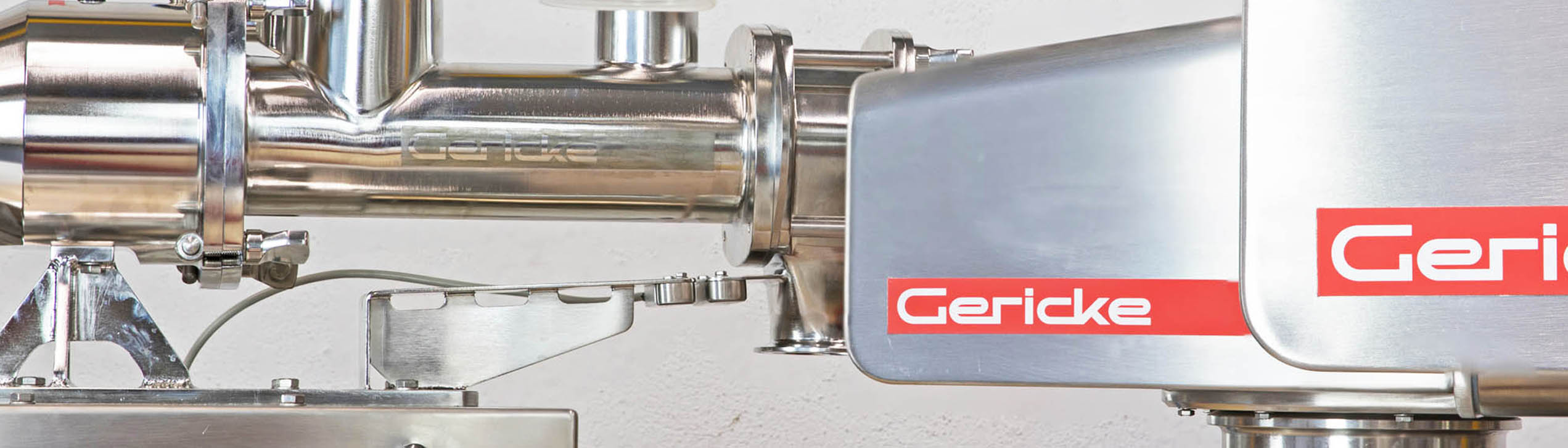
Continuous Manufacturing
Advancing Pharma Manufacturing with Gericke Solutions
Discover how Gericke’s modular machines, advanced control systems, and high containment capabilities can transform your pharmaceutical manufacturing processes. Our solutions ensure efficiency, quality, and adaptability, perfectly aligning with the industry's shift towards continuous manufacturing. With over 125 years of expertise and comprehensive testing, Gericke is your partner in revolutionizing production processes.
For more information:
InquiryRevolutionize OSD Manufacturing with Continuous Processes
For years, traditional batch processes have dominated oral solid dosage (OSD) manufacturing. However, the FDA and European Medicines Agency now recognize the significant benefits of continuous manufacturing. This regulatory shift has removed barriers, paving the way for the adoption of continuous feeding and blending in drug production.
Whether you're ready to implement continuous manufacturing processes or are exploring this innovative technology, we offer tailored solutions to meet your unique requirements.

Quality by Design for Pharmaceutical OSD
Discover the unparalleled advantages of Gericke machines, designed to transform your manufacturing processes. Our solutions cater to diverse industry needs, ensuring efficiency, quality, and adaptability.
Key Benefits of Gericke Machines:
- Modular Design: Accommodates various processed materials and throughputs.
- Integration: Supports up to 7 feeders for complex formulations.
- Advanced Control System: Guarantees highest product quality and reduced waste.
- Open Automation Interface: Compatible with PAT-management and Advanced Process Controllers.
- High Containment: Up to OEB 5.
- Optimized Access: Enables fast cleaning and product changes with minimal downtime and high containment.
- Compact Mixer: Ideal for low throughputs with minimal startup losses and adaptable residence time and energy input.

Latest Technology in Continuous Manufacturing
Additionally, our modularity allows for tailoring to your specific requirements and seamless integration into existing lines. Gericke’s formulation skid GFS ensures smooth integration with various downstream processes such as:
- Direct Compression
- Wet or Dry Granulation
- Hot Melt Extrusion
- Sachet or Capsule Filling
- Or as an individual unit operation for formulation development
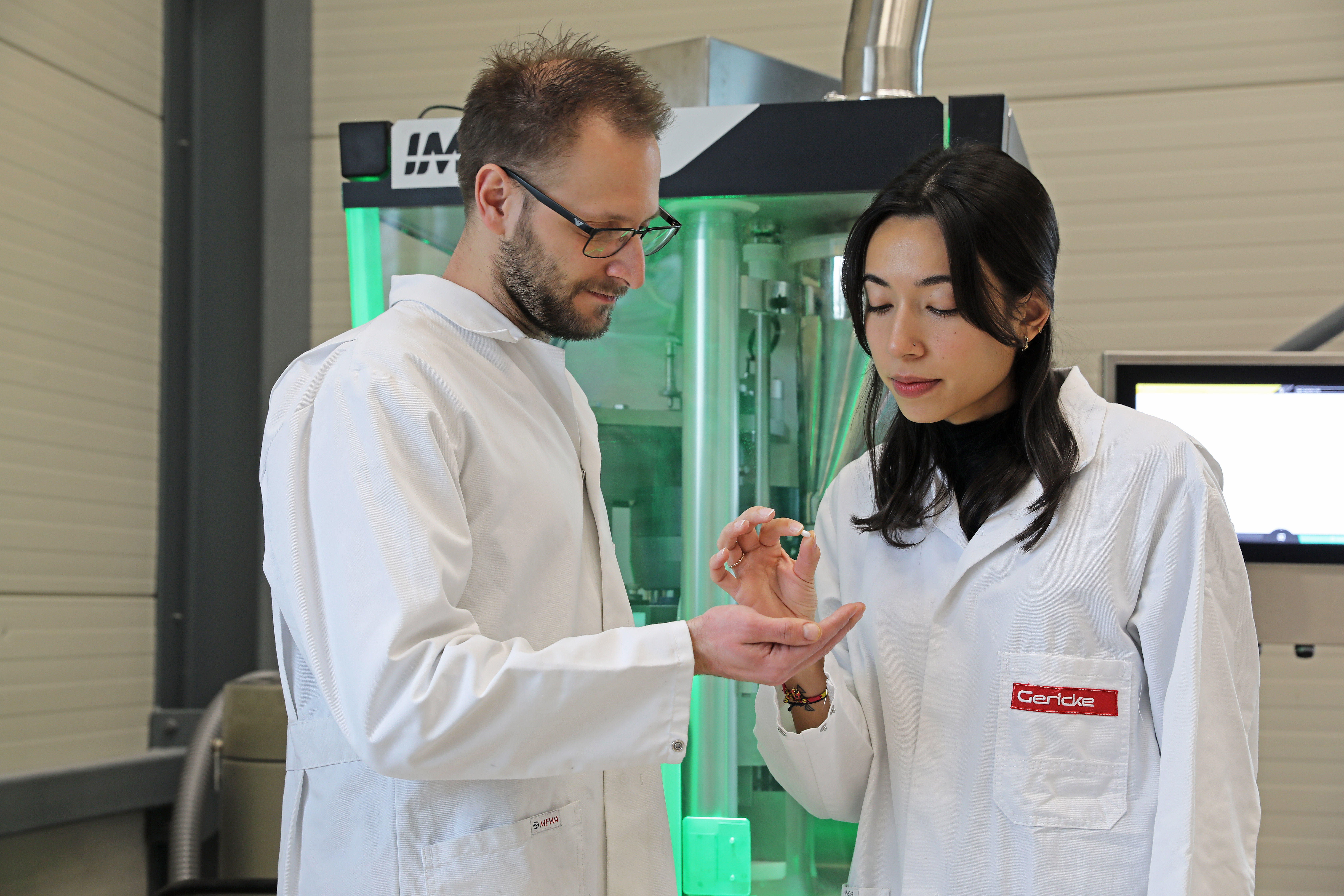
Shorten Research and Development Time
Leverage over 125 years of powder handling expertise to enhance your continuous OSD production. Gericke experts guide you through every project phase, from choosing a continuous production system to seamless integration, ensuring maximum efficiency.
- Consulting Services: Our experts assist in selecting and integrating continuous production systems.
- State-of-the-Art Test Centers: Evaluate our systems with your specific materials to ensure they meet your unique requirements.
- Tailored Testing: Our specialists design and perform tests tailored to your needs, checking performance and accuracy per NAMUR NA40.
- Machine Interaction Testing: Test machine interactions and gain valuable insights.
- Sampling Services: We provide sampling for lab tests, market response, and customer training.
- Remote Test Monitoring: Benefit from video streaming for remote test monitoring.
For more information:
Leading Edge Powder Processing Technology